With Flowers, control risks and hazards for zero-defect production scheduling
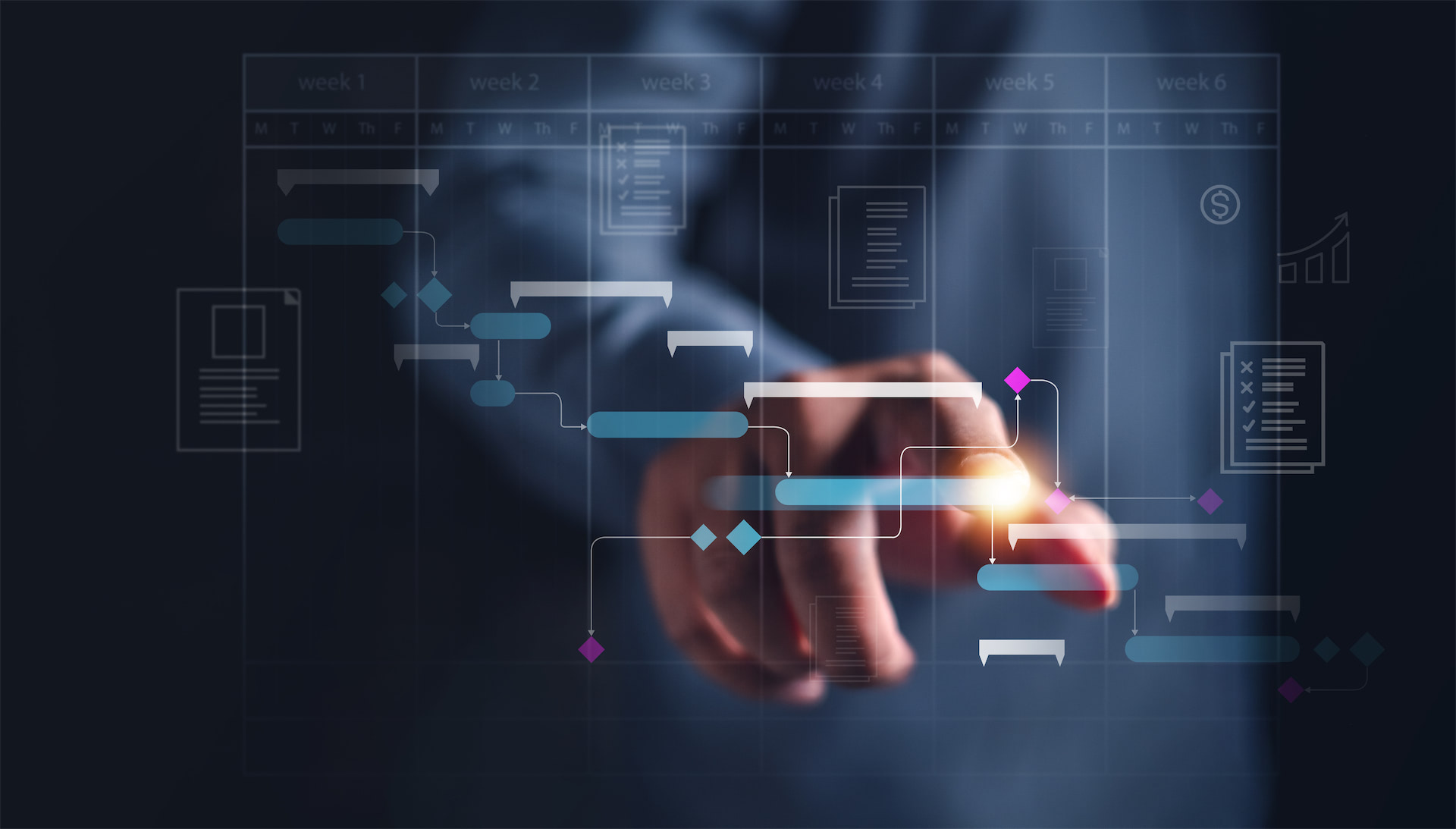
Your scheduling is optimized whatever your manufacturing processes
While planning aims to manage resources, raw materials, intermediate products and capacities in the medium and long term, scheduling has a much finer temporal granularity and deals with the sequencing and coordination of day-to-day operations.
In short, it involves managing material flows and coordinating operations in near real time, while taking into account internal and external hazards and uncertainties.
Depending on the type of manufacturing process, the scheduling approach can be based on flow simulation or on constraint resolution techniques.
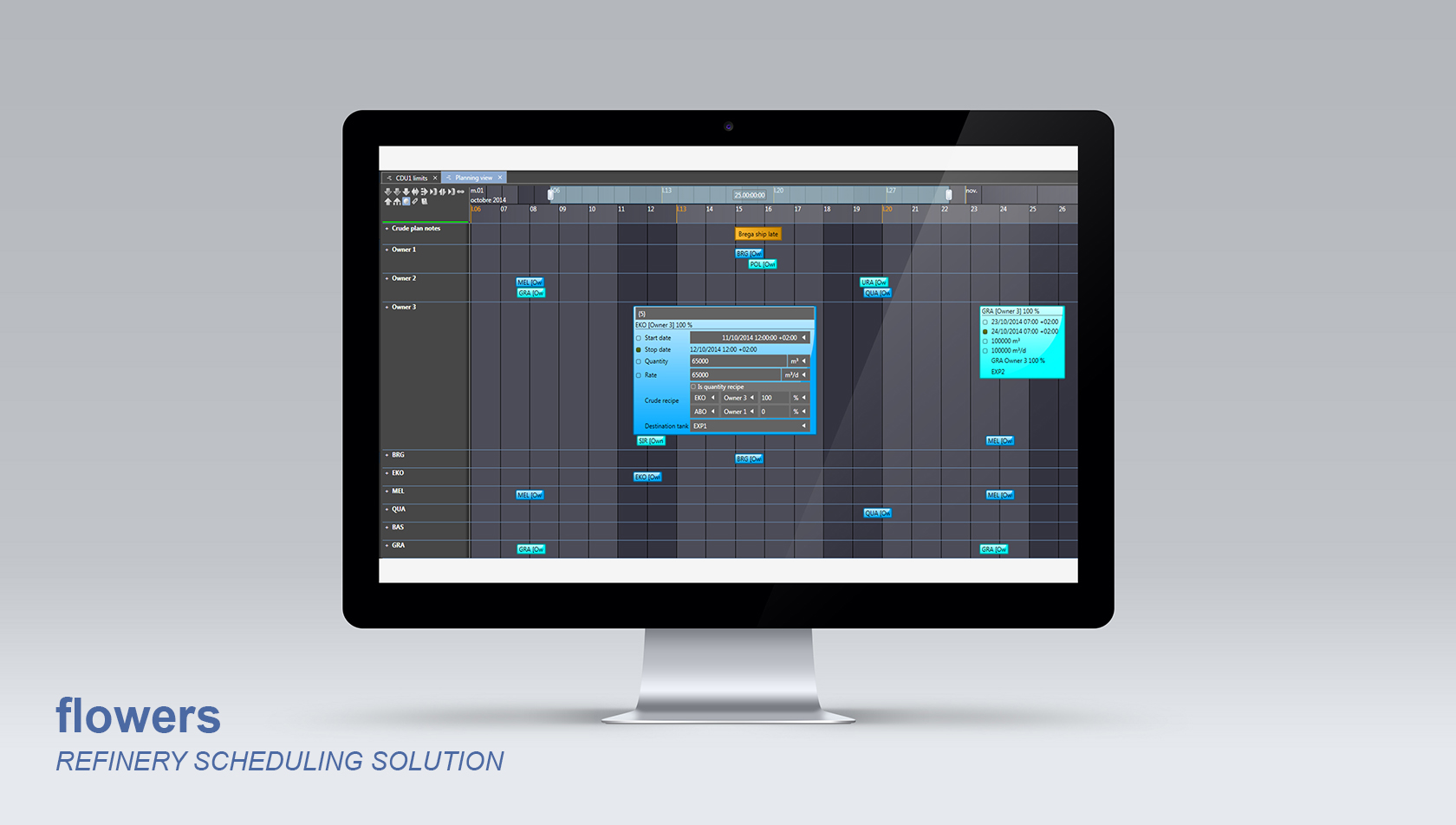
In continuous flow processes
Where equipment operates 24 hours a day, 7 days a week, flow simulation, coupled with ergonomic user interfaces, is most appropriate. It allows fluid interaction of the user with the system, so as to enable them to find a feasible schedule through trial and error. One of the objectives of scheduling such a process is to ensure the continuity of operations in all circumstances.
In batch type processes
(batch production), production is done in campaigns, and there is often a significant cost linked to campaign changes. Furthermore, the need to satisfy demand requires having sufficient quantities of products in stock to avoid launching new campaigns with each new demand. The objective of scheduling is then to find the right trade off between the costs of changing campaigns and that of immobilizing assets in the form of high stocks: this is an optimization problem.
In made-to-order manufacturing processes
(Make to Order, MTO), scheduling is generally done following a specific order from the customer. A flow simulation approach may be suitable here to ensure dynamic scheduling which requires great flexibility.
To sum up
The Flowers platform provides both efficient discrete event simulation capabilities, as core functionality, and constraint resolution and local optimization capabilities through a specialized module.
The simulation engine is available to all scheduling users and makes it possible to calculate the consequences of choices which are either made by the user himself or generated by the optimization module. In the latter case, the user will be able to manually modify the generated solution and simulate the final operation sequence before validating it.
The other standard features of the platform are also available, including:
- Advanced, fluid graphics that enable quick analysis and adjustment of scenarios
- Complete recording of results
- Exploration, comparison and archiving of numerous scenarios
- Multi-user operation…